We answer your questions
At Check and Go, we understand the needs and concerns of fruit and vegetable distribution companies. That’s why we have gathered the most common questions to clarify how our service can help you optimize the supply chain,ensure product quality and reduce environmental impact.Find everything you need to know about our comprehensive solution here.
FAQ
How does Check and Go ensure that products meet the quality standards required by supermarkets?
We conduct objective and thorough inspections at the origin, following visual and organoleptic specifications, labeling, size, weight, and more, ensuring that each shipment meets the customer's quality requirements.
What advantages does the Check and Go seal bring to my supply chain?
The seal reduces the need for intensive inspections at the destination, minimizes rejections, food waste, and additional costs, while improving logistical efficiency and enabling products to go directly to the store shelves.
What types of certifications support Check and Go's services?
We are backed by ISO 17020 accreditation for origin inspections, ISO 17025 for analysis, and IFS Logistics standard for transportation, along with other international certifications that ensure food safety and quality.**
**What percentage of products are inspected before shipment?**
We inspect a minimum of 2% of the sales units (UDV) and adjust this percentage according to the specific needs of each client.
What information will I receive after the quality inspection?
You will receive a detailed, real-time report with the inspection results, allowing you to make quick decisions and ensure that the merchandise is ready for shipment.
How does Check and Go ensure safety during transportation?
We use airtight sealing systems, pest control measures, and real-time temperature monitoring via GPS and thermographs, ensuring optimal conditions throughout the entire journey.
**How does Check and Go help reduce rejections and food waste?**
By inspecting at the origin, we ensure that only suitable products are shipped, minimizing claims, product destruction, and environmental impact.
**What happens if non-conformities are detected during the origin inspection?**
If we detect products that do not meet the established standards, we immediately notify the client so they can take corrective actions before shipment, preventing rejections at the destination.
Is it possible to customize inspections according to my company's needs?
Of course, we adapt our processes to each client's specifications, ensuring a personalized service that meets the required quality standards.
How can I access the inspection and transportation reports?
The reports are automatically sent in real-time through digital platforms, providing quick and easy access to all relevant information about each shipment.
What economic benefits does Check and Go bring to my company?
Our service reduces costs associated with claims, product destruction, and last-minute replacements, optimizing your logistics and ensuring greater profitability in the supply chain.
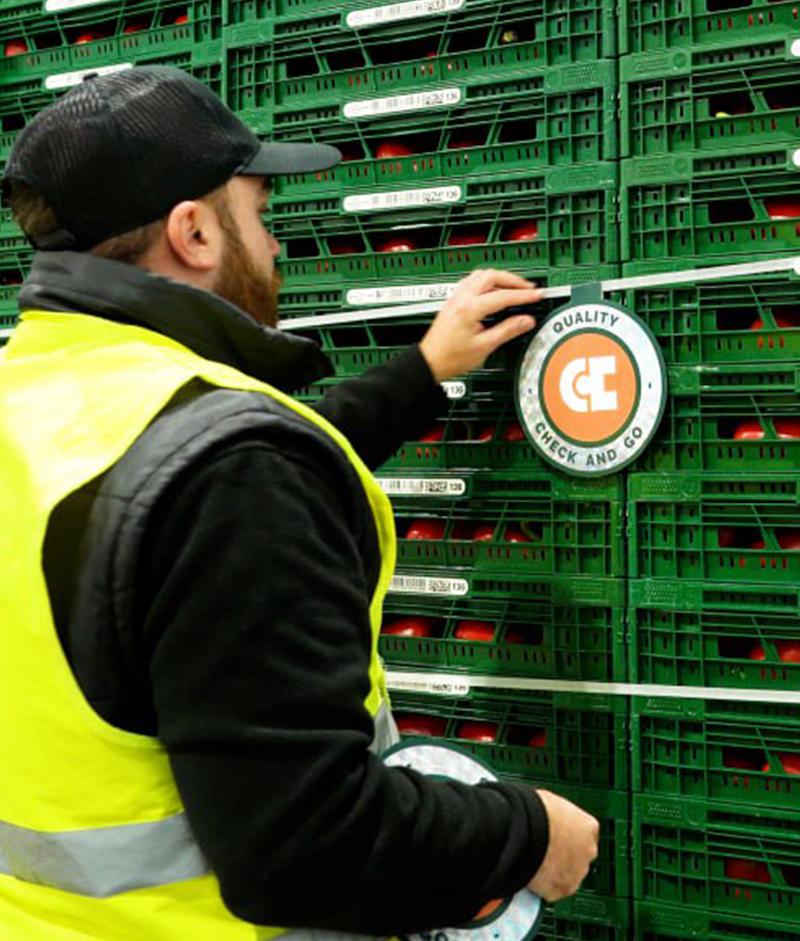
With Check and Gowe take quality and safety in the fresh produce supply chain to a new level. Our service combines origin inspections with controlled transportation and storage, ensuring that every product meets the highest standards from the very first moment until it reaches its destination.
By implementing this system, you not only optimize time and resources but also reduce the risk of rejections, enhancing operational efficiency and guaranteeing customer satisfaction.
Want to know all the details? Contact us and discover how Check and Go can transform your logistics and make a difference in your business.
Quality Check and Go
Quality. Safety. Efficiency.
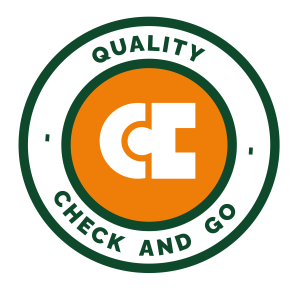